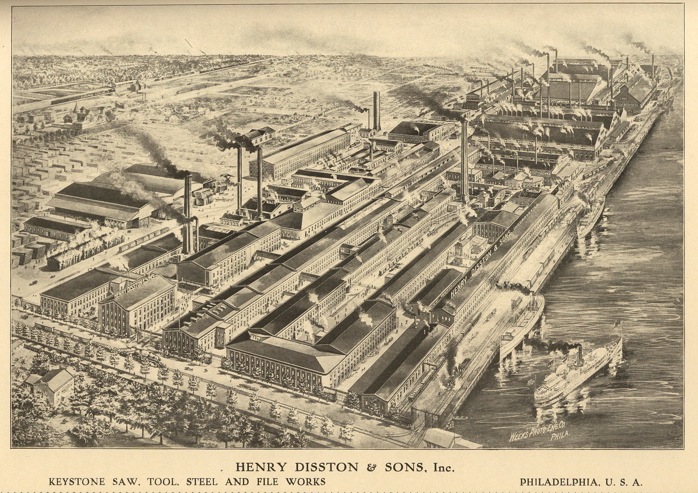
© Philadelphia Year Book, 1917.
Disston and Sons, Keystone Saw Works, 1872-
6700-6800 State Road & 5100-5200 Unruh Street, Philadelphia PA 19135
(between Unruh Street and Princeton Avenue, east of State Road to the Delaware River)
© Harry C. Silcox, Ed.D.,
Workshop of the World (Oliver Evans Press,
1990).
At its zenith, Henry Disston
and Sons employed an average of 2,500 workers, covered
sixty-four acres, and comprised sixty-four buildings.
Until its sale to H.K. Porter in 1955, it was a
family-run firm. It had sales branches in nine cities,
including Tokyo, and a plant in Canada. The largest saw
manufacturer in the world, Disston and Sons also produced
files, tools of all types, springs, and steel plate, as
well as special steel jobs. The company's Keystone
trademark on a product indicated high-quality to all who
knew the reputation of the firm. 1
Saws remained Disston's best known product throughout its
existence; indeed every imaginable sort of blade for
cutting wood or metal was produced at the saw works. The
process of creating a handsaw blade involved eighty-two
steps. It began with the making of steel in crucible pots
which were poured into molds that produced ingots. The
ingots originally were flattened by screw-type vices;
later steam pressured hammers were used. The process of
flattening continued in the rolling mills, where large
sections of rolled steel plate were routinely turned into
saw plate steel. After teeth were cut in the steel "in
the soft," the metal was tempered in a precision furnace
before hardening in a bath, it was then heated again in a
tempering oven and allowed to cool naturally. Tempering
gave the steel elasticity (spring) and durability. The
next step was "smithing,"—hand-hammering the blade
to perfect flatness and subjecting it to several stages
of grinding and filing. The trademark then was etched on
the blade and the teeth were set by angling every other
tooth to the left or the right. Thus, when the saw was in
use, the teeth cut a channel slightly larger than the
width of the blade, which prevented the blade from
binding in the channel.
Disston produced wooden saw handles and the brass screws
with which they were attached to the blades. This process
involved eighteen steps. Handles were made from applewood
logs, which were first cut to the proper thickness and
then aged in the open air for three years. The applewood
was then "ripped" cut, marked to pattern, sawed inside
and outside, oiled, nose-fonned, sanded, varnished,
carved, polished, bored, and split. Finishing the handles
was one of the few jobs that women performed in the
Disston works, (the company employed 195 women and 2,605
men in 1916). 2
During its peak years ofproduction, Disston used some
35,000 files per year to sharpen saws. Thus, file-making
machines and mechanical sharpening machines were
important components of the Disston plant. Files, like
saws, demanded the best hard steel available. The steel
ingots for the files received a slightly different
treatment in the rolling mills than those used to produce
saws. The file ingots were reheated and rolled into large
bars. These bars were cut into pieces, which in turn were
rolled into bars of decreased diameter and increased
length until they formed the size of file required. Once
the desired thickness and widths were reached, the strip
of steel traveled to the file works where it was cut into
proper lengths. The file blank was then "tanged," the
tang being the smooth, pointed end on a file which is
usually fitted with a handle, although frequently it
could be employed without a handle. This was done by
heating one end of the file and forging a tang from it.
The worker in this operation was seated before an
automatic hammer with a small furnace close at hand. The
temperature in the file oven was crucial to this
operation, as too much heat would prevent the file from
being properly teethed and too little heat would not
allow the workman to successfully mold the tang.
The files were put into air-tight boxes and placed in
annealing ovens, which were set to a predetermined
temperature. Once removed from the oven, the files cooled
in the boxes, not in the open air. These processes caused
the file to warp, or become uneven, so that it then had
to be taken to the straightening department, and thence
to the grinding department where the files were made
perfectly smooth so that teeth could be cut evenly into
them. The teeth were then cut into the soft metal with a
chisel-like machine, and a final heating hardened the
file. In all, Disston produced 50 types of files, some
flat, some rounded, and with variable teeth that ranged
from the rasp file to a fine file for aluminum.
3
The Disston plant site is divided by Knorr Street into
two main components. North of the Knorr Street gate on
New State Road are the steel and power plants, and the
rolling mills, to the south are the offices and
production buildings. The steel plant consists of an
armor-plate building, a steel-fumace building, and
rolling mills. The armor-plate building had large dies
that stamped out plates of steel for tanks in World War
II. Making steel required raw iron and steel scraps which
were stored in a large yard located next to the steel
furnace building. The crucible pot method was used to
melt the ore and scraps to form ingots. Adjacent to the
steel-fumace building were the rolling mills, where the
steel ingots were rolled into sheets of steel. The stack
on the power plant, which dominated the Tacony landscape
for years, was destroyed by an explosion in 1951 when
workmen did not properly blow out the gas fumes from the
stack before igniting the furnace. Except for the rolling
mills and the annor-plate building, these structures are
empty shells today.
The area south of Knorr Street is far more complicated to
describe, it contains a jumble of varied buildings, some
dating back to the 1872-1878 era. These include
grindstone sheds, a hardening shop, lumber yard, file
forge building, jobbing building, machine building, and
production buildings for hand saws, long saws, circular
saws and band saws. With the exception of the lumber yard
and the grindstone sheds most of these buildings are
still standing today.
A small part of the site south of Knorr Street remains
industrially active under ownership of Disston R.A.F.
Industries. This company produces large circular saws for
cutting hot steel. A small hardening shop, a torch-steel
cutting shop, and a teeth-cutting and smithing shop
function daily. More than twenty employees work under the
direction of Roland Woehr. However, this factory at New
State Road south of the Knorr Street gate is a shell of
the once mighty Disston and Sons Keystone Saw
Works. 4
1 Harry C. Silcox,
"Henry
Disston and Sons 1840-1955: The Rise and Fall of
America's mightiest Saw Works," unpublished manuscript,
(Philadelphia, 1989).
2 Philip Scranton and
Walter Licht, Work
Sights, Industrial Philadelphia, 1890-1950
, (Philadelphia,
1986), pp. 170-181.
3 "The
File, Its History and Making," The Disston Crucible: A
Magazine for the Millman, (January, February, March,
April, 1914), [available at the Free Library of
Philadelphia, Logan Square, Philadelphia].
4 Interview with Bob
Bachman and Roland Woehr at Disston and Sons site by
Harry C. Silcox, December 27, 1988.
Update May
2007 (by
Torben Jenk):
Many buildings remain, but most are in poor shape.
The buildings
along the north side of Unruh Street include decorative
cast iron "star bolts" (describing their common
shape)which are here shaped like keystones with the
letter 'D' within, a clear reference to Disston and the
Keystone Saw Works. Stacks of grinding stones are visible
where Unruh Street meets the Delaware River, some stuck
together with concrete and formerly used as a bulkhead.
Truck and auto repairs seem to be the only use today. It
appears that the buildings directly north of those along
Unruh have been demolished. Farther up State Road, at
#6795, is the entrance road to Disston Precision and the
rest of the former Disston complex. The wall along State
Road to the north is made of sandstone, possibly from
used grinding stones. On the south side you get the best
idea of the campus of two-story brick buildings. To the
left are 20th century buildings, tall single-story metal
structures, mostly vacant. Farther east along the
Delaware River is a finer collection of used grinding
stones.
Most impressive
is the steel furnace building with a date stone that
reads, '1940.' Only forty feet of the chimney remains
beside this robust building. Ovalized iron flues pierce
the roof-like glassless skylights, while the interior is
gutted and rotting.
Farther west is the rolling mill, identified by a date
stone that reads '1936', and shows a keystone and a
roller in relief. An auto scrap yard occupies the space
to the north.
Disston Precision
is still in operation and makes huge saw blades, valve
components, press plate, clutch components, shredder
knives and slitters. Disston offers the following
services: heat treating, flattening, grinding, laser
cutting, plasma burning, waterjet cutting, precision
machining and fabrication.
Other tenants include Marjam, which distributes building
materials; and American Lighting and Signalization, which
installs and maintains roadway lighting, traffic
signalization, airport lighting, street lighting,
interstate signing, and underground and overhead utility
lines.
There is talk of adapting the Disston complex for loft
apartments, and commercial and office space. Most of the
other industrial sites along the Delaware have or will be
demolished. The complex at Disston offers an opportunity
and challenge for a creative developer who wants to offer
something more enticing than the two-thousand vinyl-clad,
vanilla box townhouses being proposed just north and
south.
To the north of Disston, on the south side of Princeton
Street, was the Tacony Army Plating Plant, built in 1941
with the mission of making plates for tanks in WWII. The
200,000-square-foot building remained open through the
1970s and officially closed in 1983. At a cost of $10
million, the US Army Corps of Engineers demolished the
building in 2004. The site was sold at auction for $2.5
million and plans exist for 407 residences to be known as
"Tacony Pointe." A small park is along the Delaware River
with a public access Tacony Boat Launch. Just north of
Princeton Street, along the Delaware, is the Quaker City
Yacht Club, a private club for boating enthusiasts and
social members, established in 1887. It leases land from
the adjacent and still operating St. Vincent's Orphan
Asylum, which is shown on the 1895 Bromley Atlas (plate
48). The same plate shows the “American Wire Glass
Mfg. Co. of Frank Shuman.
Resources:
Harry C. Silcox, "A
Place To Live and Work, The Henry Disston Saw Works and
the Tacony Community of Philadelphia"
(Pennsylvania
State University Press, University Park, PA, 1994).
Hexamer General Survey #707-708 (1873)
"Henry Disston & Sons' Tacony
Works."
Hexamer General Survey #955 (1875) "Henry
Disston & Sons' Tacony
Works."
Hexamer General Survey #1266 (1878) "Henry
Disston & Sons' Tacony
Works."
Hexamer General Survey #1407 (1879) "Henry
Disston & Sons' Tacony
Works."
Hexamer General Survey #1763-1764 (1883)
"Henry Disston & Sons' Tacony
Works."
© Edwin T.
Freedley, Philadelphia
and its Manufactures (1867), p. 306.