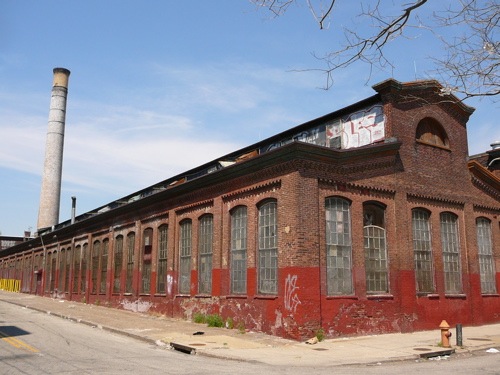
Northwest corner Estaugh & J Streets.
Luithlen Dye Corporation, c.1880-2003
Ward Elicker Casting, 2004-
J Street between Estaugh & Tioga, Philadelphia PA 19134
© Carmen A. Weber, Irving
Kosmin, and Muriel Kirkpatrick, Workshop of the World (Oliver
Evans Press, 1990).
In the 1880s Ludwig B.
Luithlen established a dye works in rented space in
Kensington. Sometime around 1895, he moved to a one story
brick dye house on the corner of J and East Estaugh
Streets in the Harrowgate section. The firm served the
large numbers of textile industries located in Kensington
throughout the twentieth century; despite the decline in
these industries, it still continues to operate.
Although the Luithlen name is still associated with the
dye works, it has operated under several families in the
twentieth century. Under Emil Viet, the dye works
employed twnty-nine males and an office work force of
four people in 1916. 1
Viet ran the
Luithlen Dye Works until 1919. At that date, the Wiegand
family acquired the company. The firm employed between
sixty and forty-two people in the 1940s.
2
Incorporating in 1948, Louis Wiegand, Jr. is now the
third generation to operate the company. The one story
brick building, with a monitor along its roof line, holds
forty-four dye kettles. Narrow fabrics, yarns, carpet,
bindings, tapes, and zippers are dyed in these kettles,
which are heated by steam supplied by two 500 horsepower,
oil fired boilers. The two story brick building on the
corner of Tioga and J Streets holds storage space as well
as the finishing department and drying room. The drying
operation utilizes steam to operate a range, ten dryers,
and twelve yarn winders. 3
1 Department of Labor
and Industry, Pennsylvania, 1916, p. 1286.
2 Chamber of Commerce
and Board of Trade, Philadelphia, p. 39.
3 Interview with Louis
Weigand, Jr., President, (October 27, 1988).
East facade along
J Street.
Undated map
(<1900) showing "L.B. Luithlen Dye House" on the
northwest corner of Estaugh & J Streets. Tioga Street
is at the top, Kensington Avenue is on the diagonal.
Collection of Ward Elicker Casting.
Sections &
Elevations of the Dye House for Luithlen Dye Works drawn
by William Steele & Sons, April 15, 1920. Collection
of Ward Elicker Casting.
Plan of Luithlen
Dye Works by Factory Insurance Association, 1973.
Collection of Ward Elicker Casting.
"Anyone Jumping
The Curb Or Driving On The Pavement Will Be Prosecuted"
— sign along Estaugh Street.
"$10.00 REWARD For the
Arrest & Conviction Of Anyone Defacing This
Property!" — sign along Estaugh Street.
Update May
2007 (by
Torben Jenk):
Luithlen Dye was sold to
Wayne Mills in 2003, which then moved the dyeing
operations to Manyunk.
The
site was sold and is now occupied by Ward Elicker
Casting. For the SIA June 2007 conference,
Jeb Wood, CEO and
Metalsmith of Ward Elicker Casting, offered a tour of the
foundry and explained the entire process of translating
an artist’s work (often in clay) into a finished
sculpture in bronze or iron. Known as “lost wax
casting” the process involves making the mould,
making the wax casting, chasing the wax, spruing, casting
the ceramic mould, burn out, casting, break out,
sandblasting, assembly, chasing, glass beading, polish,
patina, waxing, mounting and inspection. Elicker Casting
serves emerging artists (some rent space in the building)
and renowned contemporary sculptors like Tom Otterness,
Julian Schnable, George Segal and Kiki
Smith.
Most of the
dyeing equipment has been removed to accommodate the new
sculpture foundry, Ward Elicker Casting.
Ceramic shell
molds are being burned out to remove the wax. Molten
bronze will be poured into these shells.
Some Civil War
monuments were cast in "white bronze" (cast zinc).
Examples like this were cast in large numbers, only the
face being personalized. Now deteriorating, Ward Elicker
Casting can take new molds and cast these monuments again
in long-lived real bronze.
A brief
history of sculpture and casting in Philadelphia.
(Torben Jenk
2007)
More than just making machines, Philadelphia has a
centuries old tradition of supporting the arts and
artists. In 1795, the first public monument in
Philadelphia was installed over the entrance to the
Library Company of Philadelphia, a marble figure of Ben
Franklin. The Pennsylvania Academy of Fine Arts, founded
in 1805, is the nation’s oldest art museum and
school of fine art. In 1872, concerned citizens who
believed that art could play a role in a growing city
formed the Fairmount Park Art Association to purchase,
commission and maintain art works from the world’s
leading sculptors including Daniel Chester French, Paul
Manship, Frederick Remington, Jacques Lipschitz, Henry
Moore and all three generations of the Calder family:
Alexander Milne, Alexander Stirling and Alexander
“Sandy.” Thousands of artworks, large and
small, abstract and commemorative, are displayed
throughout the city.
Philadelphia’s most
famous sculpture, “William Penn” stands atop
City Hall. Sculpted by Alexander Milne Calder, it is
thirty six feet tall and weighs 53,000 pounds -- the
largest single piece of sculpture on any building in the
world. The Tacony Iron Works started casting it in
1890 and the bronze sculpture was set in place in 1894.
For
the past twenty five years graduates of the Pennsylvania
Academy of the Arts, the University of the Arts, Temple
University and other art programs have sought experience
and training in the comprehensive Johnson Atelier in
Hamilton, NJ, founded by J. Seward Johnson who believed
“There is no art more dependent on it’s
technical aspects than sculpture. An ignorance of
technique limits a sculptor’s creativity, wastes
hours of work in bringing a cast to likeness of the
original, and renders the artist captive of the
foundry’s trade secrecy and commercialism. Until
the Industrial Revolution, however, the opposite was
true. The home of the foundry was the sculptor’s
studio where the results of poor practices and errors in
judgement were immediately visited upon the artist, for
it was the artist who created and cast their own work.
This system led to quality and efficiency.”
Johnson wanted to
“restore the link and the interplay which used to
exist between the sculptor and the founding of their
work” with the goal “to educate and train
more artisans to be available to aid the sculptor in
completing their task, to develop methods for making
these processes less costly and more responsive to the
sculptor’s needs, and finally, to play a small part
in whatever forces must come together to bring more
sculpture into the 20th century lifestyle.”
When the Johnson
Atelier was reorganized a few years ago some of their
highly skilled staff artists and artisans built their own
small foundries in Philadelphia.